Seed Processing
Seed Processing
Seed Processing
Oilseeds
At Lambton Intelense, we bring next-generation AI technology and decades of expertise to optimize oilseed processing.
From soybeans, rapeseeds, sunflower seeds, and cottonseeds to flaxseeds, mustard seeds, groundnuts, sesame, safflower, and palm kernels, our state-of-the-art solutions ensure maximum yield, efficiency, and quality at every stage of production.
The process
The process
Intake
The raw seeds are received, inspected, and unloaded into intake hoppers. Conveyors, elevators, or pneumatic systems transport the seeds to storage or processing sections
Handling
The seeds are transported within the processing plant using bucket elevators, screw conveyors, and belt conveyors to ensure smooth movement between different processing stages while minimizing damage and contamination.
Know more
Drying
The moisture content of seeds is reduced using rotary dryers or seed dryers to prevent spoilage, improve storage stability, and enhance further processing efficiency.
Know more
Storage
Processed seeds are stored in silos or storage bins under controlled conditions to maintain quality, prevent moisture absorption, and ensure a steady supply for further processing or packaging.
Know more
Weighing
Seeds are accurately measured using weighing scales and precise amounts are fed into the next processing stage
Know more
Cleaning
Aspirator uses airflow to remove light impurities such as dust, husks, and chaff from seeds, ensuring cleaner raw material. Gravity Separator then sorts seeds based on density, eliminating immature, damaged, or low-quality seeds using vibration and airflow. To prevent machinery damage and maintain purity, a Hopper Magnet captures and removes metal contaminants before further processing.
Know more
Dehulling
The outer hulls of seeds are removed using dehullers to improve processing efficiency and product quality. This step helps in better oil extraction and reduces fibre content in the final product.
Know more
Hull Separation
Removed hulls are separated from the kernels using aspirator to ensure product purity and prevent contamination in further processing.
Know more
Flaking
Seeds are pressed into thin flakes using flaking mills or roller mills, increasing the surface area for better oil extraction and improving the efficiency of further processing.
Know more
Intake
The raw seeds are received, inspected, and unloaded into intake hoppers. Conveyors, elevators, or pneumatic systems transport the seeds to storage or processing sections
Handling
The seeds are transported within the processing plant using bucket elevators, screw conveyors, and belt conveyors to ensure smooth movement between different processing stages while minimizing damage and contamination.
Know more
Drying
The moisture content of seeds is reduced using rotary dryers or seed dryers to prevent spoilage, improve storage stability, and enhance further processing efficiency.
Know more
Storage
Processed seeds are stored in silos or storage bins under controlled conditions to maintain quality, prevent moisture absorption, and ensure a steady supply for further processing or packaging.
Know more
Weighing
Seeds are accurately measured using weighing scales and precise amounts are fed into the next processing stage
Know more
Cleaning
Aspirator uses airflow to remove light impurities such as dust, husks, and chaff from seeds, ensuring cleaner raw material. Gravity Separator then sorts seeds based on density, eliminating immature, damaged, or low-quality seeds using vibration and airflow. To prevent machinery damage and maintain purity, a Hopper Magnet captures and removes metal contaminants before further processing.
Know more
Dehulling
The outer hulls of seeds are removed using dehullers to improve processing efficiency and product quality. This step helps in better oil extraction and reduces fibre content in the final product.
Know more
Hull Separation
Removed hulls are separated from the kernels using aspirator to ensure product purity and prevent contamination in further processing.
Know more
Flaking
Seeds are pressed into thin flakes using flaking mills or roller mills, increasing the surface area for better oil extraction and improving the efficiency of further processing.
Know more



Intake
The raw seeds are received, inspected, and unloaded into intake hoppers. Conveyors, elevators, or pneumatic systems transport the seeds to storage or processing sections
Handling
The seeds are transported within the processing plant using bucket elevators, screw conveyors, and belt conveyors to ensure smooth movement between different processing stages while minimizing damage and contamination.
Know more
Drying
The moisture content of seeds is reduced using rotary dryers or seed dryers to prevent spoilage, improve storage stability, and enhance further processing efficiency.
Know more
Storage
Processed seeds are stored in silos or storage bins under controlled conditions to maintain quality, prevent moisture absorption, and ensure a steady supply for further processing or packaging.
Know more
Weighing
Seeds are accurately measured using weighing scales and precise amounts are fed into the next processing stage
Know more
Cleaning
Aspirator uses airflow to remove light impurities such as dust, husks, and chaff from seeds, ensuring cleaner raw material. Gravity Separator then sorts seeds based on density, eliminating immature, damaged, or low-quality seeds using vibration and airflow. To prevent machinery damage and maintain purity, a Hopper Magnet captures and removes metal contaminants before further processing.
Know more
Dehulling
The outer hulls of seeds are removed using dehullers to improve processing efficiency and product quality. This step helps in better oil extraction and reduces fibre content in the final product.
Know more
Hull Separation
Removed hulls are separated from the kernels using aspirator to ensure product purity and prevent contamination in further processing.
Know more
Flaking
Seeds are pressed into thin flakes using flaking mills or roller mills, increasing the surface area for better oil extraction and improving the efficiency of further processing.
Know more
The Lambton Advantage



Precision automation
Our AI-powered systems analyze real-time data on moisture levels, kernel density, and oil content, enabling precision processing and improving oil recovery rates.
By leveraging predictive analytics, we help you reduce energy consumption and optimize resource usage, lowering your operational costs.



Optimum quality assurance
Our AI-driven systems monitor kernel size, moisture, and temperature, ensuring consistent flake thickness for superior oil extraction.
Our digital systems offer real-time monitoring and traceability, ensuring compliance with industry standards and providing full batch transparency.
Our AI-driven systems monitor kernel size, moisture, and temperature, ensuring consistent flake thickness for superior oil extraction.
Our digital systems offer real-time monitoring and traceability, ensuring compliance with industry standards and providing full batch transparency.
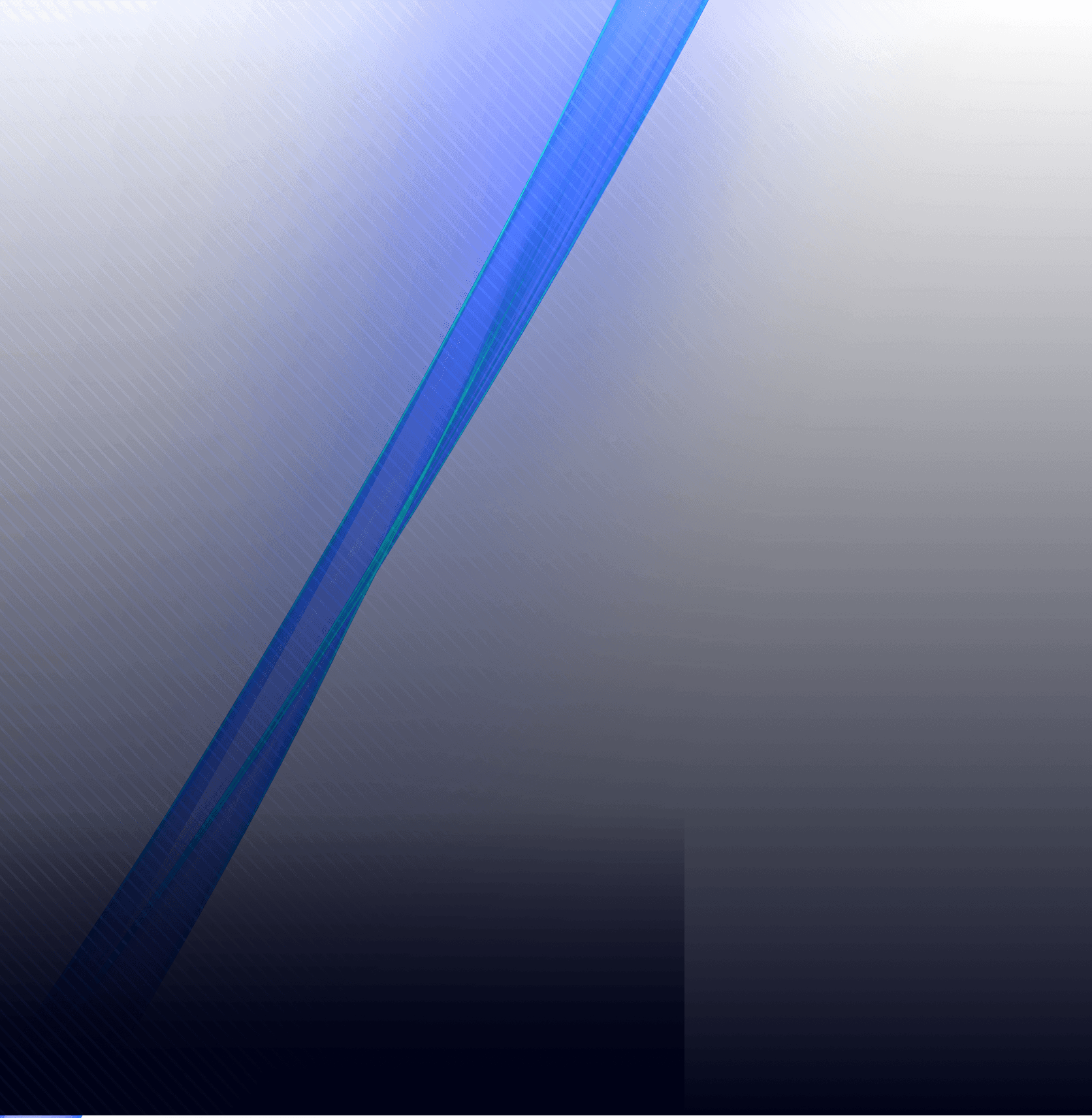
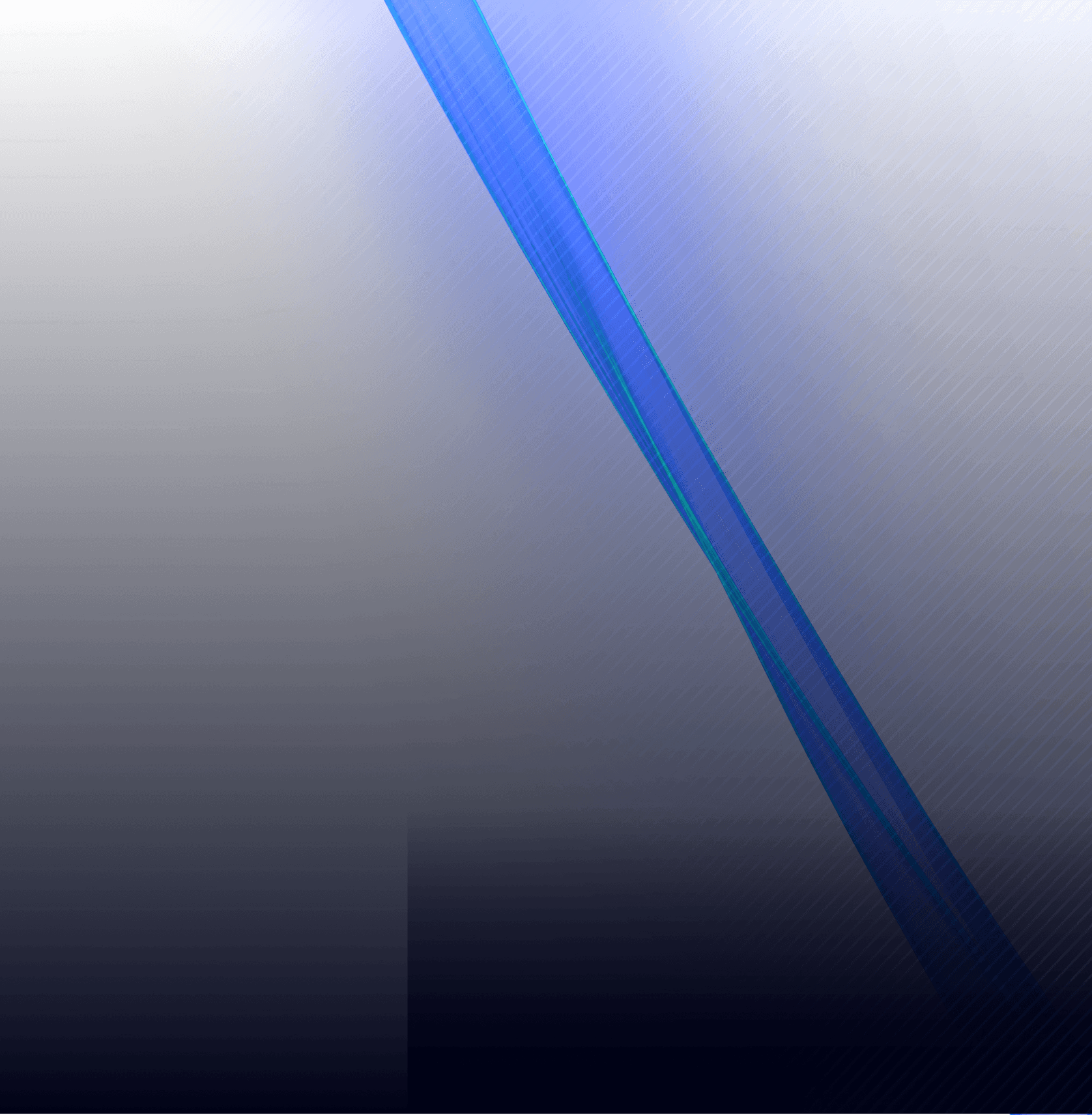
Stay updated with Us
Dive into our blog for expert insights, tips, and industry trends to elevate your project management journey.
Customized design
Ongoing support
Fast delivery
No spam, just genuine updates!