Mills
Mills
Mills
Rice and Paddy
Our technology encompasses every aspect of rice and paddy processing – from pre-cleaning and paddy storage to dryers, hullers, polishers, rice whiteners, optical sorters, and bagging systems.
By integrating AI and advanced technology, we can accurately assess quality, moisture content, and other critical grain attributes. This data-driven approach allows for precise adjustments throughout the process, ensuring optimal quality and consistency.
As a result, our systems are scalable, adaptable to different stages of consumption, and capable of meeting the demands of various markets while maintaining the highest standards of product integrity.
Our technology encompasses every aspect of rice and paddy processing – from pre-cleaning and paddy storage to dryers, hullers, polishers, rice whiteners, optical sorters, and bagging systems.
By integrating AI and advanced technology, we can accurately assess quality, moisture content, and other critical grain attributes. This data-driven approach allows for precise adjustments throughout the process, ensuring optimal quality and consistency.
As a result, our systems are scalable, adaptable to different stages of consumption, and capable of meeting the demands of various markets while maintaining the highest standards of product integrity.
The process
The process
The process
Pre-cleaning
Removes impurities like sticks from incoming raw materials, protecting downstream equipment and improving mill efficiency. It often combines scalping and air washing for effective separation.
Fine-cleaning
Paddy is fed into the huller machine from a buffer hopper or storage bin. The paddy passes through rubber roll hullers or steel hullers that apply pressure to break and remove the husk.
Classifier
Gravity Separator
Hulling
Paddy is fed into the huller machine from a buffer hopper or storage bin. The paddy passes through rubber roll hullers or steel hullers that apply pressure to break and remove the husk.
Hulling Machine
Paddy Separation
Then Paddy Separators separate any unhulled grains and send them back for another hulling cycle.
Brown Rice → Sent to the whitening/polishing section.
Mixed Grains → Passed through the separator again for better separation.
Paddy → Sent back to the huller for reprocessing.
Paddy Separator
Whitening
Brown rice is whitened in a whitener machine, where friction or abrasive rollers remove the bran layers while an aspiration system or sieves separate the loosened bran. The whitened rice then moves to a tip separator before polishing for final cleaning before grading and packaging.
Whitener Machine
Tip Separation
Separates materials based on shape and size using rotating indented cylinders. It provides precise sorting for seed cleaning and grain grading.
Tip size Grader
Polishing
After the tip separation process (where small broken tips of rice grains are removed), polishing is done to enhance the appearance and texture of rice.
Polishing Machine uses water, polisher and friction to smooth the rice surface, giving it a glossy, shiny finish.
Color Sorting
After polishing, rice enters the color sorter, where high-speed cameras scan each grain for discoloration or defects. If an unwanted grain is detected, an air ejector removes it instantly. The cleaned, uniform rice then moves to final grading and packaging.
Color Sorter
Length Grading
Sort materials based on length, separating broken rice and final rice. It improves product uniformity by creating a consistent size.
Length Grader
Storage
After sorting, broken rice and final (head) rice are stored separately in bins to maintain quality and facilitate packaging.
Day Bins
Machine Buffer Bins
Silo Aeration Tiles
Bagging and Stitching
Rice is measured and filled into bags (25kg, 50kg, or custom sizes) using an automated or manual bagging machine and are weighed for accuracy, and excess rice is adjusted before sealing.
Bags are stitched using industrial sewing machines to ensure they are securely closed.
Online Weigher
Weighing & Bagging Machine
Pre-cleaning
Removes impurities like sticks from incoming raw materials, protecting downstream equipment and improving mill efficiency. It often combines scalping and air washing for effective separation.
Fine-cleaning
Paddy is fed into the huller machine from a buffer hopper or storage bin. The paddy passes through rubber roll hullers or steel hullers that apply pressure to break and remove the husk.
Classifier
Gravity Separator
Hulling
Paddy is fed into the huller machine from a buffer hopper or storage bin. The paddy passes through rubber roll hullers or steel hullers that apply pressure to break and remove the husk.
Hulling Machine
Paddy Separation
Then Paddy Separators separate any unhulled grains and send them back for another hulling cycle.
Brown Rice → Sent to the whitening/polishing section.
Mixed Grains → Passed through the separator again for better separation.
Paddy → Sent back to the huller for reprocessing.
Paddy Separator
Whitening
Brown rice is whitened in a whitener machine, where friction or abrasive rollers remove the bran layers while an aspiration system or sieves separate the loosened bran. The whitened rice then moves to a tip separator before polishing for final cleaning before grading and packaging.
Whitener Machine
Tip Separation
Separates materials based on shape and size using rotating indented cylinders. It provides precise sorting for seed cleaning and grain grading.
Tip size Grader
Polishing
After the tip separation process (where small broken tips of rice grains are removed), polishing is done to enhance the appearance and texture of rice.
Polishing Machine uses water, polisher and friction to smooth the rice surface, giving it a glossy, shiny finish.
Color Sorting
After polishing, rice enters the color sorter, where high-speed cameras scan each grain for discoloration or defects. If an unwanted grain is detected, an air ejector removes it instantly. The cleaned, uniform rice then moves to final grading and packaging.
Color Sorter
Length Grading
Sort materials based on length, separating broken rice and final rice. It improves product uniformity by creating a consistent size.
Length Grader
Storage
After sorting, broken rice and final (head) rice are stored separately in bins to maintain quality and facilitate packaging.
Day Bins
Machine Buffer Bins
Silo Aeration Tiles
Bagging and Stitching
Rice is measured and filled into bags (25kg, 50kg, or custom sizes) using an automated or manual bagging machine and are weighed for accuracy, and excess rice is adjusted before sealing.
Bags are stitched using industrial sewing machines to ensure they are securely closed.
Online Weigher
Weighing & Bagging Machine


Pre-cleaning
Removes impurities like sticks from incoming raw materials, protecting downstream equipment and improving mill efficiency. It often combines scalping and air washing for effective separation.
Fine-cleaning
Paddy is fed into the huller machine from a buffer hopper or storage bin. The paddy passes through rubber roll hullers or steel hullers that apply pressure to break and remove the husk.
Classifier
Gravity Separator
Hulling
Paddy is fed into the huller machine from a buffer hopper or storage bin. The paddy passes through rubber roll hullers or steel hullers that apply pressure to break and remove the husk.
Hulling Machine
Paddy Separation
Then Paddy Separators separate any unhulled grains and send them back for another hulling cycle.
Brown Rice → Sent to the whitening/polishing section.
Mixed Grains → Passed through the separator again for better separation.
Paddy → Sent back to the huller for reprocessing.
Paddy Separator
Whitening
Brown rice is whitened in a whitener machine, where friction or abrasive rollers remove the bran layers while an aspiration system or sieves separate the loosened bran. The whitened rice then moves to a tip separator before polishing for final cleaning before grading and packaging.
Whitener Machine
Tip Separation
Separates materials based on shape and size using rotating indented cylinders. It provides precise sorting for seed cleaning and grain grading.
Tip size Grader
Polishing
After the tip separation process (where small broken tips of rice grains are removed), polishing is done to enhance the appearance and texture of rice.
Polishing Machine uses water, polisher and friction to smooth the rice surface, giving it a glossy, shiny finish.
Color Sorting
After polishing, rice enters the color sorter, where high-speed cameras scan each grain for discoloration or defects. If an unwanted grain is detected, an air ejector removes it instantly. The cleaned, uniform rice then moves to final grading and packaging.
Color Sorter
Length Grading
Sort materials based on length, separating broken rice and final rice. It improves product uniformity by creating a consistent size.
Length Grader
Storage
After sorting, broken rice and final (head) rice are stored separately in bins to maintain quality and facilitate packaging.
Day Bins
Machine Buffer Bins
Silo Aeration Tiles
Bagging and Stitching
Rice is measured and filled into bags (25kg, 50kg, or custom sizes) using an automated or manual bagging machine and are weighed for accuracy, and excess rice is adjusted before sealing.
Bags are stitched using industrial sewing machines to ensure they are securely closed.
Online Weigher
Weighing & Bagging Machine
The Lambton Intelense Advantage



End-to-end expertise
End-to-end expertise
End-to-end expertise
Our team of food technologists and engineers combines deep industry knowledge with the latest technological advancements.
We understand the complexities of rice and paddy processing — from pre-cleaning and dehusking to polishing and sorting — and design solutions that prioritize food safety, quality, and yield optimization.
Our team of food technologists and engineers combines deep industry knowledge with the latest technological advancements.
We understand the complexities of rice and paddy processing — from pre-cleaning and dehusking to polishing and sorting — and design solutions that prioritize food safety, quality, and yield optimization.
Our team of food technologists and engineers combines deep industry knowledge with the latest technological advancements.
We understand the complexities of rice and paddy processing — from pre-cleaning and dehusking to polishing and sorting — and design solutions that prioritize food safety, quality, and yield optimization.



Real-time precision
Real-time precision
Real-time precision
Using AI and big data analytics, our digital services provide real-time insights into rice quality, moisture content, and impurity levels.
Our technology ensures seamless monitoring, helping you reduce waste, increase yield, and enhance efficiency. Whether you're handling bulk storage, milling, or packaging, our solutions ensure consistent quality across every stage.
Using AI and big data analytics, our digital services provide real-time insights into rice quality, moisture content, and impurity levels.
Our technology ensures seamless monitoring, helping you reduce waste, increase yield, and enhance efficiency. Whether you're handling bulk storage, milling, or packaging, our solutions ensure consistent quality across every stage.
Using AI and big data analytics, our digital services provide real-time insights into rice quality, moisture content, and impurity levels.
Our technology ensures seamless monitoring, helping you reduce waste, increase yield, and enhance efficiency. Whether you're handling bulk storage, milling, or packaging, our solutions ensure consistent quality across every stage.
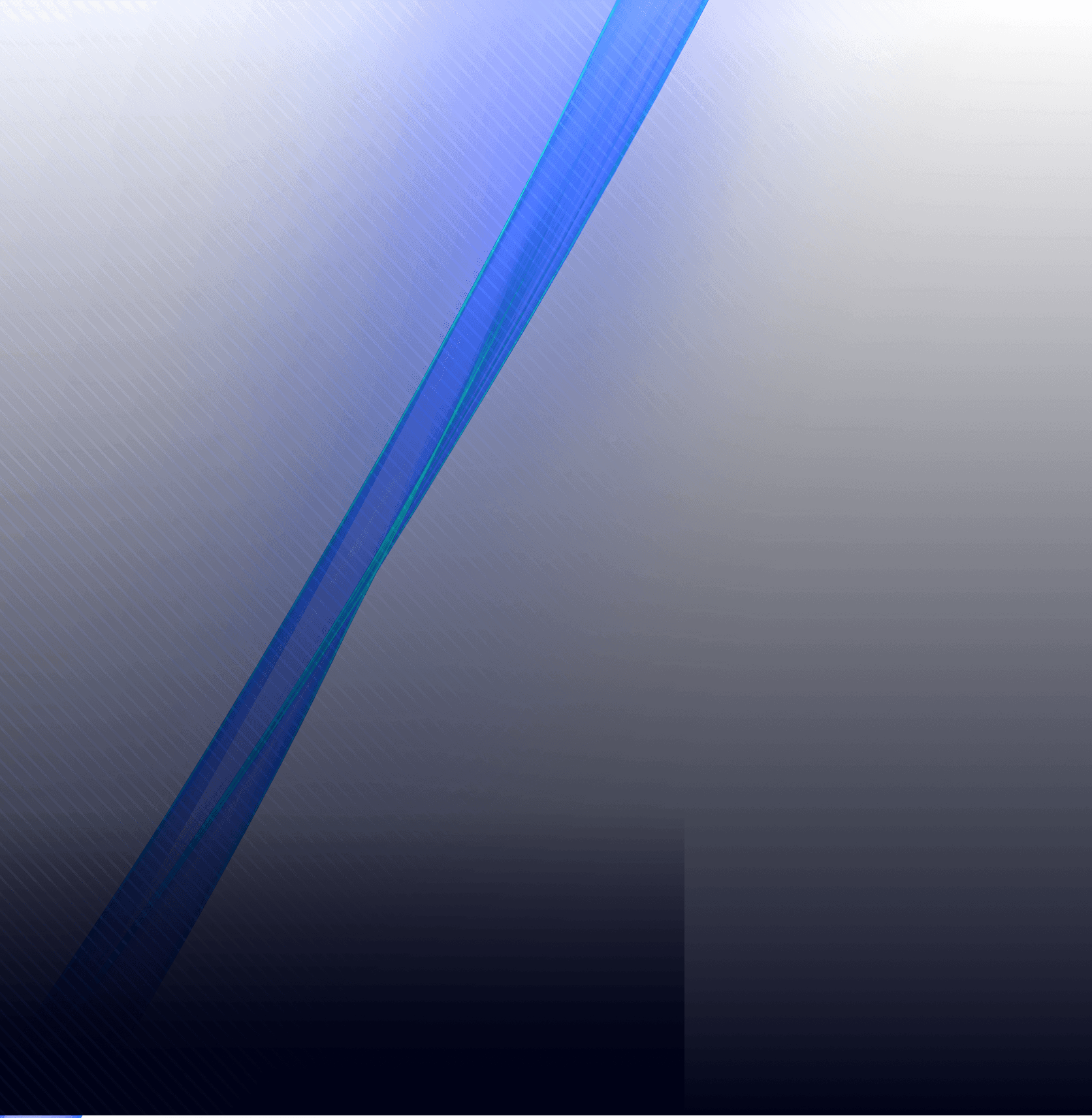
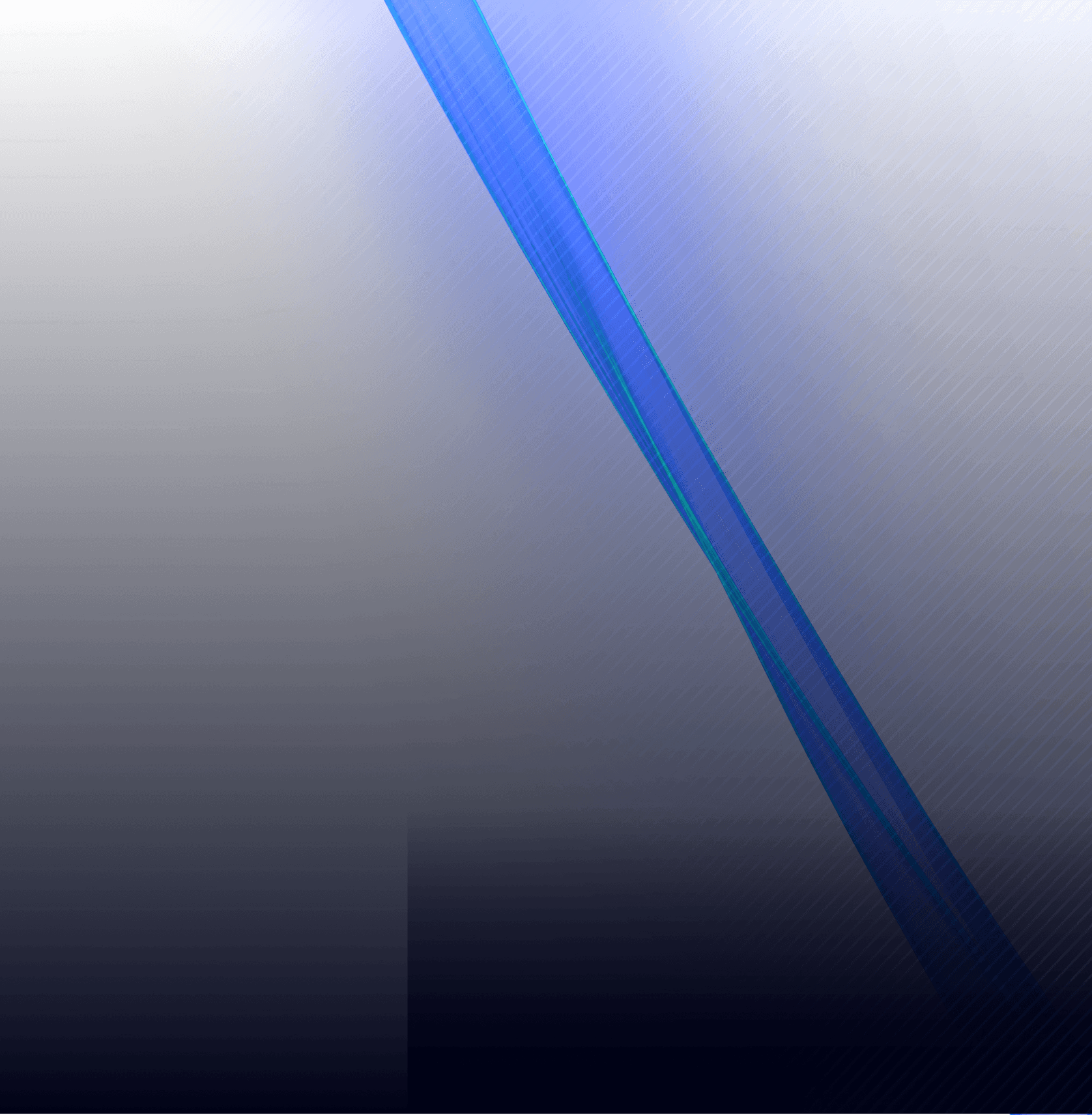
Stay updated with Us
Dive into our blog for expert insights, tips, and industry trends to elevate your project management journey.
Customized design
Ongoing support
Fast delivery
No spam, just genuine updates!